Sugar mill lotus rollers are also called perforated rollers. These are modern sugar mill rollers that are used for juice extraction. They have modern internal drainage systems and better material composition. Furthermore, lotus rollers have advanced manufacturing techniques. These techniques have increased the strength and longevity of these rollers.
Sugar mill lotus rollers are energy-efficient, too. Thus, perforated rollers, also known as lotus rollers, are becoming the industry’s attraction. Powerline Magazine stated that sugar mills in India have largely replaced conventional rollers with Sugar Mill Lotus Rollers. The main aim behind this was to become more energy-efficient.
Finished Sugar Mill Lotus Roller
What Is a Sugar Mill Lotus Roller?
Sugar Mill Lotus rollers are also called perforated rollers. They are a type of modern top roller that is used to crush sugarcane. They have numerous precisely engineered holes on their surface. Furthermore, unlike typical rollers that rely on grooves, Sugar Mill Lotus Rollers draw juice through their bodies. This improved drainage system reduces the juice reabsorption and increases juice extraction.
Key features of Sugar Mill Lotus Roller
Features of Sugar Mill Lotus Roller
Read More: How to Buy a Sugar Mill Roller: The Ultimate Guide for Sugar Mill Owners
Sugar Mill Lotus Rollers have the following key features:
- Holes on the Surface
Multiple holes are drilled precisely across the rollers surface. These holes are conical or tapered in shape and they widen towards the interior of the roller. During the crushing, these holes provide an additional pathway for juice collection. Furthermore this internal drainage reduces the threat of juice reabsorption.
- Internal House Drainage System:
All the surface holes are connected to an internal network of channels. The extracted juice travels through these channels out of the machine.
- Surface Groovings:
Groovings are the special patterns that are cut on the roller’s surface. Sugar Mill lotus rollers also contain these grooves, like all other typical rollers. These grooves help in cane gripping, facilitating juice drainage and collecting the fiber blanket.
Performance Comparison with Solid Rollers
Sugar Mill Solid Rollers Comparison with Sugar Mill Lotus Rollers
Read More: Vertical Sugar Mill Rollers | Complete Information
Sugar Mill Lotus Rollers Design Process Step by Step
The design of the sugar mill lotus roller is broken down into the following components: Body Material, Perforation and Drainage System, Surface Grooving and Texture, Structural Considerations, Shaft Integration and Bearing Design.
Roller Body Material
Sugar Mill Lotus Rollers are mostly manufactured from custom-casting steel. It specifically contains low to medium carbon steels, ranging from 0.25% to 0.50% C. Additional elements can be added to enhance the lotus roller’s characteristics. The additional components include:
- Manganese: It increases strength, hardness, and wear resistance. It is useful in absorbing impact loads.
- Chromium: It improves hardness, wear resistance, and corrosion resistance. It is useful in hard-facing layers or the base metal for tougher applications.
- Nickel: It increases toughness, ductility, and strength, particularly at high temperatures.
- Molybdenum: It increases strength and hardenability. It helps refine the grain size.
- Vanadium / Niobium / Titanium: It is added in small quantities. It helps to refine grain size and improve strength.
Material Composition Of a Sugar Mill Lotus Roller
Benefits of Steel Sugar Mill Lotus Rollers
Benefits of Steel Sugar Mill Lotus Rollers
Lotus Rollers are made from custom-cast steel, which has the following benefits.
- Superior Strength and Toughness:
Steel Sugar Mill Lotus Rollers provide larger crushing forces. This means the lotus rollers exert more pressure for better juice extraction. Furthermore, as the steel is tougher, there is reduced risk of damage. This prevents sudden failures and expensive emergency shutdowns.
- Enhanced Durability
Sugar Mill Lotus Rollers have a greater potential to absorb large pressures. This means the longevity of the groove pattern is increased. Furthermore, steel shows higher weldability characteristics. This means that the layers don’t crack off easily.
- Improved Repairability
A sugar mill steel lotus roller can easily be welded when it is cracked or damaged. This saves immense time and money. This ability means that the lifespan of a steel lotus roller is increased before it needs replacement.
- Resistance to Fatigue
Sugar mill steel lotus rollers have a higher fatigue limit. This means they are less likely to fail unexpectedly due to fatigue. It reduces downtimes and operational failures.
Perforation and Drainage System
The entire efficiency of Sugar Mill Lotus Rollers lies in its efficient drainage system. This drainage system is precisely engineered to prevent juice absorption and increase juice extraction.
Drainage Features of Sugar Mill Lotus Rollers
Hole Geometry:
The holes are precisely designed and drilled to optimize the juice flow. Holes are either tapered or conical in shape. They are narrow on the outer surface and wider on the inside of the roller. These holes have a slightly elliptical cross-sectional area. These holes facilitate juice flow and minimise clogging.
Hole Alignment and Distribution
The holes are arranged in helical or staggered patterns across the surface of the lotus roller. Manufacturers should make sure that a balanced number of holes are drilled. Too few will limit drainage, and too many will compromise the roller’s strength.
The holes are situated between the crest and trough of the external grooves. The combination of external grooves and holes creates an efficient drainage system.
Precision Manufacturing
Advanced machining techniques, such as precise drilling and CNC machining, are used to calculate hole size, shape, and alignment.
Juice extraction optimization
Working Operation of Lotus Rollers In Sugar Mills
Read More: What’s a Sugar Mill Roller? Sugarcane Crushing Guide
The core function of sugar mill lotus rollers is to provide an efficient juice drainage system. It is ensured using the following ways:
- Combating Re-absorption
The holes of the Lotus Roller provide an active drainage system. During crushing, the juice is forced directly into these holes before the bagasse can reabsorb it. This increases the juice extraction efficiency.
- Enhanced Juice Flow
The combination of external grooves and internal perforations provides multiple channels. The juice escapes from the mill using these channels. There is no limitation for drainage, so more cane is now processed.
- Improved Bagasse Quality:
As more juice is extracted, the collected bagasse is drier. This drier bagasse is a more efficient boiler fuel.
Prevention of clogging and back-pressure
Sugar Mill Lotus Rollers have overcome the challenges of clogging and back-pressure. This is due to the following reasons.
- Tapered Hole Design
The conical shape of the hole mainly prevents clogging. If any particle enters the smaller outer diameter, it will have enough space to pass through. It is because the diameter increases towards the interior. This prevents particles from clogging the roller’s hole.
- Effective Internal Drainage Channels:
The internal channels are designed to be smooth and wide. They ensure a smooth flow of juice from the holes to the discharge points. This prevents any blockages.
- Periodic Cleaning:
Modern sugar mills maintain regular checks for all roller surfaces. This prevents unexpected failures or blockages.
Surface Grooving & Texture
The outer surface of the sugar mill lotus roller is involved in crushing. The outer design is therefore very important for the efficient working of the lotus roller.
Lotus rollers’ groove types:
- Circumferential V-Grooves:
These are the most common grooves. They are cut around the circumference of the roller, perpendicular to its axis. They have a V-shape profile with a specific angle of 60 degrees. However, their depth and pitch are altered based on mill position and cane characteristics.
Circumferential V-Grooved Sugar Mill Lotus Rollers
- Helical Grooves:
These grooves are cut in a spiral or screw-like pattern along the roller. These are mostly used in feed rollers, and sometimes used in top rollers.
Helical Grooved Sugar Mill Lotus Rollers
- Chevron Grooves:
These are V-shaped grooves that run axially to the roller. They are often cut into the surface in addition to the circumferential grooves.
Chevron Grooved Sugar Mill Lotus Rollers
Surface hardening for increased life
Modern techniques are used to increase the life of sugar mill lotus rollers. These techniques include:
- Hardfacing
Hardfacing is the most commonly used and effective method. It involves welding a layer of wear-resistant alloy onto the roller’s surface. The wear-resistant alloy is typically rich in chromium, e.g., 25% to 30%.
- Induction / Flame Hardening:
Induction / Flame Hardening is a heat treatment process. It rapidly heats the surface of the roller to a very high temperature using electromagnetic induction or an open flame. After this, the roller is cooled quickly. This makes the surface microstructure very hard.
Structural Considerations
The special structural considerations of sugar mill lotus rollers ensure strength, durability and increased efficiency. Some structural considerations include:
Shell thickness optimization
The shell is the outer part of the roller that crushes the cane. The shell can be either thicker or thinner.
A thicker shell provides greater strength and reduced corrosion during the crushing. It uses more material for repeated re-grooving and hardfacing.
Thinner shells reduce the material cost and weight. However, they can limit the channels available for drainage. To improve the situation, multiple holes need to be accurately drilled on the roller’s surface.
Thick Shell Lotus Rollers Comparison With Thin Shell Lotus Rollers
Solid vs hollow cores
Sugar mill lotus rollers have an internal juice drainage system. This means that their cores are not entirely solid as compared to typical rollers.
Sugar mill lotus rollers feature a core that has juice drainage channels. This is where the juice is extracted from the mill.
If a solid core were used, the internal drainage system would be useless because there would be no available channels. Thus, lotus rollers have hollow cores. Hollow core’s strength should not be doubted. It is because the core’s remaining parts are designed and cast from high-strength steel. This ensures rigidity and load-bearing capacity.
Hollow Core Sugar Mill Rollers Comparison With Solid Core Sugar Mill Rollers
Internal cooling systems
The continuous crushing of the rollers can produce heat. Modern sugar mill lotus rollers can provide two types of cooling systems.
Circulating Fluid:
It involves a closed-loop system. The cooling fluid circulates through dedicated channels within the roller’s core. Remember that it is separate from the juice drainage system.
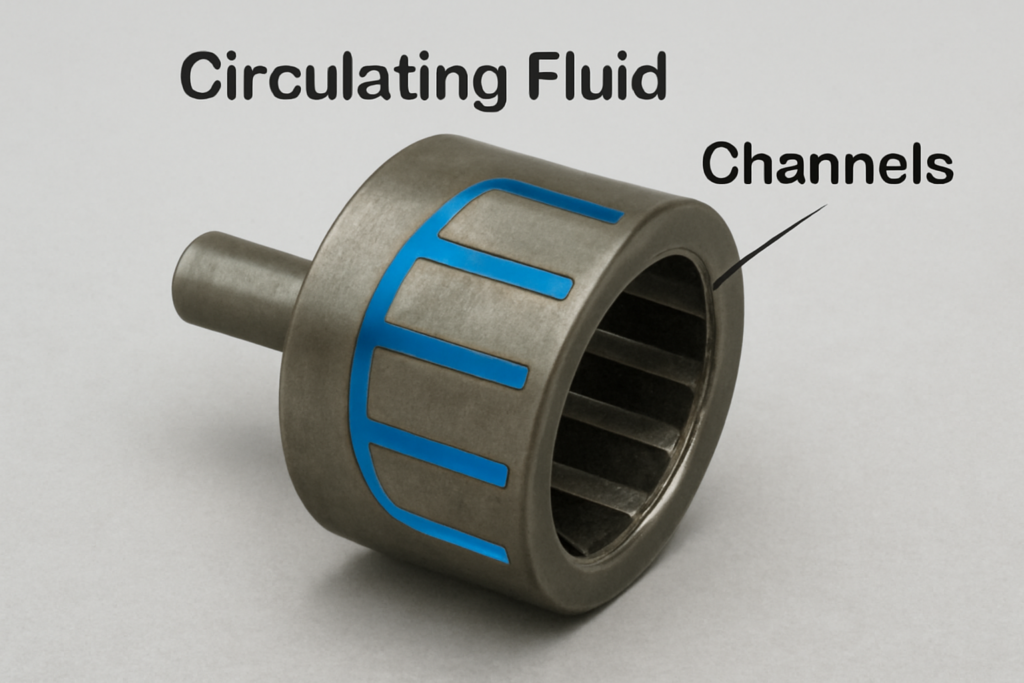
Circulating Fluid Cooling System In Sugar Mill Lotus Rollers
Heat Exchange
The fluid absorbs heat from the roller body. It then passes through an external heat exchanger to dissipate the heat before being recirculated.
Heat Exchanger Cooling System In Sugar Mill Lotus Rollers
Read More: Understanding Sugar Cane Rollers: Design, Performance, and Maintenance
f. Application-Specific Customization
Sugar Mill Lotus Rollers need application-specific customization to match the demands of individual sugar mills. The lotus rollers should adjust to mill capacity, cane types and juice recovery targets.
Adjusting to Mill Capacity
- Diameter: Larger diameter sugar mill lotus rollers provide higher capacity cane crushing. Larger diameters also provide a broader cane blanket.
- Hole Count: Higher capacity Mills target higher holes drilled with a specific pattern.
- Drainage Channel: The width of the drainage channel is kept according to the mill’s capacity. An accurate channel gap ensures efficient drainage and prevents blockages.
- Material: Custom casting steel is standard. However, very high-capacity mills can add additional elements, as covered above, to increase the lotus rollers’ strength.
- Integration with Drive Systems: The design of the roller should relate to the mill’s drive system. Only this way, accurate connections and gearings will be possible.
Adjusting to Cane Type
- The characteristics of the sugarcane being crushed influence Lotus Roller design:
- High Fiber Cane: Rougher grooves will be required for cane with higher fiber content.
- Cane Hardness: Harder cane will require a high-strength lotus roller to crush the cane and prevent corrosion. Soft cane is enriched in juice, so it will need wider channels.
- Juice Purity: Very thick juice may drain more slowly. For this, wider channels will be required.
- Impurity Levels: Mills that process dirty cane require high-strength lotus rollers to prevent corrosion.
Read More: How Sugar Cane Roller Mills Work? Understanding the Core Principle
Full Manufacturing Process
CAD Design & Engineering Simulation
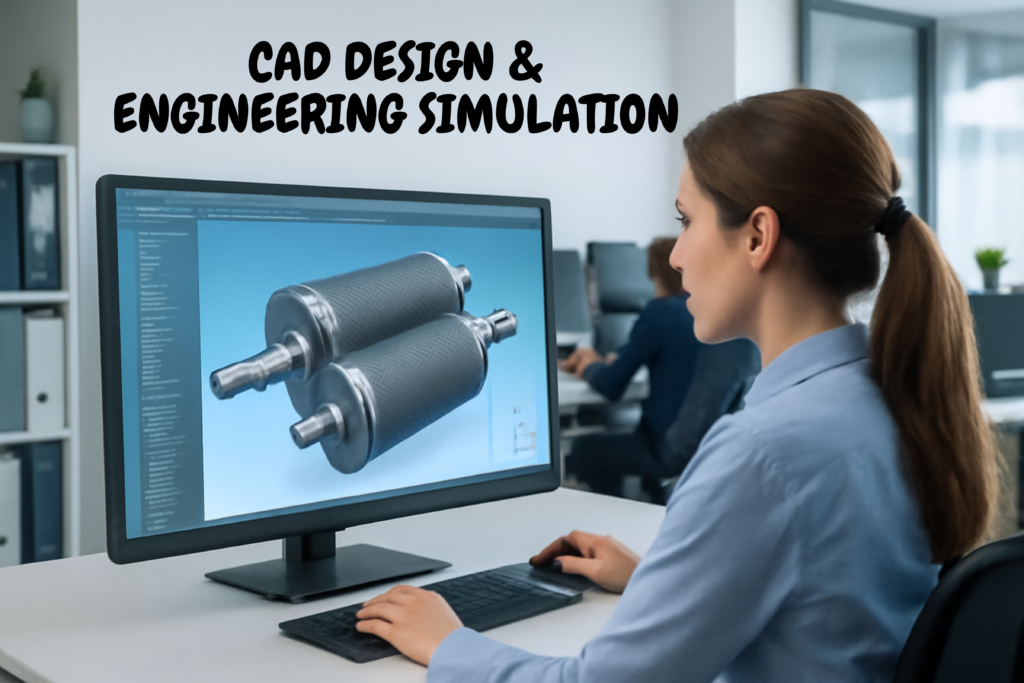
CAD Design and Engineering Stage in Manufacturing of Sugar Mill Lotus Rollers
A computer software is used to create 3D models of sugar mill lotus rollers. It helps to visualise the model. Engineers then use Finite Element Analysis to test how the rollers will handle pressure and force. It helps to analyze the model’s working and then alter the design if required.
Mold Development & Pattern Creation
Mold Development Stage in Manufacturing of Sugar Mill Lotus Rollers
First, a sand mold is created to give the roller a specific shape. Melted metal is poured into the mold and cooled. This gives the roller its basic shape. Then, the investment casting is used for additional detailing. In this process, a wax model of the roller component is created. This wax model is dipped in a ceramic slurry and sand until a strong ceramic layer is created around it. When the shell becomes dry, it is heated again to melt the wax out of the mold. This way, the mold is made. The melted metal is poured and cooled, which creates the roller’s shape.
Steel Casting & Alloy Preparation
Steel Casting & Alloy Preparation Stage in Manufacturing of Sugar Mill Lotus Rollers
Large furnaces melt the metal at controlled temperatures. Furthermore, specific materials like carbon, chromium, and manganese are added to the metal. This improves the roller’s strength, durability and prevents corrosion.
Solidification, Shakeout & Rough Cleaning
Solidification Stage in Manufacturing of Sugar Mill Lotus Rollers
When the melted metal is poured into the mold, it is left to cool and solidify. Afterward, the mold is broken carefully. The roller is extracted and is cleaned to remove any mold remaining.
Heat Treatment
Heat Treatment / Hardening Stage in Manufacturing of Sugar Mill Lotus Rollers
Heat treatment of a sugar mill lotus roller is required to harden it. The lotus roller is heated to high temperatures and is then cooled quickly. Then the lotus roller is reheated to a lower temperature. It helps to make the lotus roller more durable and stronger.
Precision Machining & Grooving
Machining & Grooving Stage in Manufacturing of Sugar Mill Lotus Rollers
Now, CNC machines are used to add further specifications to the sugar mill lotus roller. It involves cutting grooves and drilling holes. This improves cane gripping and overall operations of the sugar mill lotus rollers.
Surface Finishing
Surface Finishing, Coating Stage in Manufacturing of Sugar Mill Lotus Rollers
The sugar mill lotus roller is coated with chrome. It helps to prevent rust. Furthermore, the lotus roller can be covered with material like carbide. This prevents them from corrosion.
Quality Testing & Dynamic Balancing
Quality Testing & Balancing Stage in Manufacturing of Sugar Mill Lotus Rollers
Now, the sugar mill lotus roller is tested to ensure its accurate workings. The roller’s dimensions and balance is checked to ensure that the lotus fits accurately and does not vibrate. Furthermore, ultrasonic tests are carried out to detect internal cracks.
Assembly & Functional Testing
Functional Testing Stage in Manufacturing of Sugar Mill Lotus Rollers
The sugar mill lotus rollers are tested with full loads before they are shipped. It helps confirm the roller’s durability and functionality.
Benefits of Steel Sugar Mill Lotus Rollers
Benefits of Sugar Mill Steel Lotus Rollers
The sugar mill lotus rollers have higher durability, wear resistance, crushing efficiency, energy efficiency and cause less vibrations.
Higher Durability and Longevity
Sugar Mill lotus rollers are made from high-strength materials, which significantly increases their lifespan. They can work under heavy loads and pressures easily. Studies suggest that lotus rollers have a 25% longer service life compared to standard rollers.
Higher Corrosion Resistance
Different alloys are added to steel in the manufacturing of sugar mill lotus rollers. These alloys prevent the corrosion of the lotus rollers. Furthermore, roller strength is further increased by induction hardening and chrome plating. Studies suggest that they result in up to 30% less corrosion compared to other rollers.
Improved Crushing Efficiency
Sugar Mill lotus rollers ensure high grip and equal pressure distribution of cane. Furthermore, the grooves,, along with holes and channels, provide an efficient juice extraction capacity. This leads to a 15-20% improvement in overall milling efficiency.
Reduced Vibration and Noise
Sugar mill lotus rollers’ precise dynamic balance ensures smoother operation. This leads to less noise and reduced stress. Studies show that decreasing vibrations lead to a 10-15% reduction in maintenance costs.
Energy Efficiency
The lotus rollers’ accurate design and balance allow them to operate more efficiently. This also decreases the energy usage of the mill. Studies suggest that the energy consumption is reduced by 5-7% when lotus rollers are used.
Conclusion
Sugar Mill lotus rollers, or perforated rollers, have increased the juice extraction for sugar mills. They have modern internal drainage, strong material composition, and advanced manufacturing techniques. The modern features of the lotus roller have increased the milling capacity, efficiency, and lifespan of sugar mill industries.
As an expert in Sugar Mill Roller Chinese Manufacturing, we offer customized sugar mill rollers. Choose us for your sugar mill rollers, which promise superior performance, high durability, and a secure future. Partner with us to enhance your mill’s productivity.
To order sugar mill rollers of any design and shape from China, you can send us an email at luomiya1@gmail.com