Sugar Mill Roller Setting means setting the accurate gap between the sugar mill rollers. This accurate gap ensures increased output, lower energy consumptions and increased efficiencies. This gap is set using MED, and work opening formulas.
Understanding Sugar Mill Roller Setting
What is Sugar Mill Roller Setting?
Sugar Mill Roller Setting means setting the accurate gap between the sugar mill rollers. This gap is called “nip”.
Accurate sugar mill roller setting is important for applying uniform pressure and reducing the energy consumption. This results in increased efficiency.
Why Are Sugar Mill Roller Setting Important?
Precise Sugar Mill Roller Setting ensures higher efficiency, lower energy consumption and increased throughput.
- Extraction efficiency
The accurate gap between the rollers applies optimum pressure to the cane. This results in the rupture of sugarcane cells and the release of cane juice.
- Lower energy consumption
An optimised sugar mill roller setting leads to sufficient crushing, accurate pressure. This leads to lower energy waste and potential mechanical stress. Eventually, lower energy is consumed.
3. Increased Output
Sugar Mill roller settings directly relate to sugarcane processed per unit time. Optimal sugar mill roller settings prevent choking and slippage. Thus, the delays are reduced and the output increases.
Important Parameters in Sugar Mill Roller Setting
Important aspects of sugar mill roller setting include adjusting MED, workopening and trashplate accurately.
What is Mean Effective Diameter and its importance in sugar mill roller setting?
The Mean Effective Diameter refers to the average working size of the roller. In other words it is the diameter of the roller that is actively engaged in the cutting process. In conclusion, MED is a calculated diameter that tells the true size that effectively grips and crushes the sugarcane.
Accurate MED in sugar mill roller setting helps us to figure out:
- The optimum speed of the sugar mill rollers
- The uniform power supplied to rollers
- The accurate roller pressure applied
How to calculate MED?
What are the Work Openings in sugar mill roller setting?
Work Openings are the specific, critical gaps within the sugar mill. They are set to control the sugarcane feed, crush the sugarcane and separate the juice from the bagasse. This means that work openings ensure proper functioning of the rollers and the overall juice extraction process.
What are the types of Work Opening?
Work Openings have three types:
- Feed Opening:
The Feed Opening is also called the entry nip or feeding opening. It is the initial gap between the rollers where the sugarcane enters first. In a three-roller mill, the gap between the Feed Roller and the Top Roller.
Its role is to feed the sugarcane into the crushing zone. Usually it has the widest gap between the rollers to allow a consistent flow of cane.
- Discharge Opening
The Discharge Opening is also known as the delivery nip or exit nip. It is the final gap between the rollers through which the crushed sugarcane exits. In a three-roller mill, this is the gap between the Top Roller and the Discharge Roller.
Its role is to maximize juice extraction. These rollers apply the highest pressure to extract the last possible amount of juice from the cane fibers. Usually it has the
- Trash plate opening
Trash plate opening is designed to collect waste material and cane fibers during the crushing process. In a three roller mill, a trash plate is a stationary curved plate placed beneath the top roller.
Its main role is to prevent reabsorption, and collect the blanket of bagasse efficiently.
What is the role of Trash Plate Setting in sugar mill roller setting?
Trash plates act as a fixed guide and a pressure point for sugar mills. They ensure the smooth crushing process of the sugarcane.
This is a picture of a typical trash plate.
- Directing Flow:
The trash plate guides the sugarcane its passageway from one nip to another. It starts by entering the sugar cane into the feed nip and ends when the cane exits from the trash plate opening.
- Maintaining Blanket Integrity:
It supports the efficient collection of the bagasse. This in return prevents the bagasse from collapsing or disorganizing between the rollers.
- Preventing Re-absorption:
The trash plate helps to physically separate the juice from the moving bagasse blanket. This prevents the juice from being reabsorbed into the fibers as they travel towards the next compression.
What is the correct positioning of trash plates?
Accurate trash plate’s position ensures optimal mill performance. A visual picture of a trash plate in a sugar mill setting is as follows.
Key aspects of correct positioning include:
- Accurate Roller Gap:
Accurate gaps between the rollers are very important. If the gap is too wide, it can lead to cane escaping the rollers or reabsorption of juice. Similarly if the gap. Similarly, a narrower gap can generate heat, consume more power and cause corrosion of the rollers.
- Angle of the Plate:
The angle of the trash plate set relative to the rollers affects the juice collection. It needs to be steep enough to allow juice to drain but shallow enough to support the bagasse blanket.
- Reduced Corrosion:
The trash plate experiences continuous friction. Accurate Trash plate position can reduce corrosion and increase the lifetime. Still frequent inspections are required for repair or replacements.
What are Mill Geometry Parameters?
Mill geometry parameters are rollers, physical dimensions and arrangements. Geometry parameters are crucial for optimised crushing, juice extraction, and overall efficiency.
What is Roller size and pitch circle?
Roller Size are the rollers dimensions. It primarily consists of rollers diameter and length.
- Diameter: Larger diameter rollers provide larger surface area for crushing.This leads to higher capacity and juice extraction.
- Length: Longer rollers are capable of processing more sugarcane per pass. This also increases capacity and efficiency.
The Pitch Circle is an imaginary circle inside each roller. It represents the diameter at which two grooved rollers gears perfectly without slippage. In simpler words it is diameter on each roller that defines how rollers synchronize and drive each other.
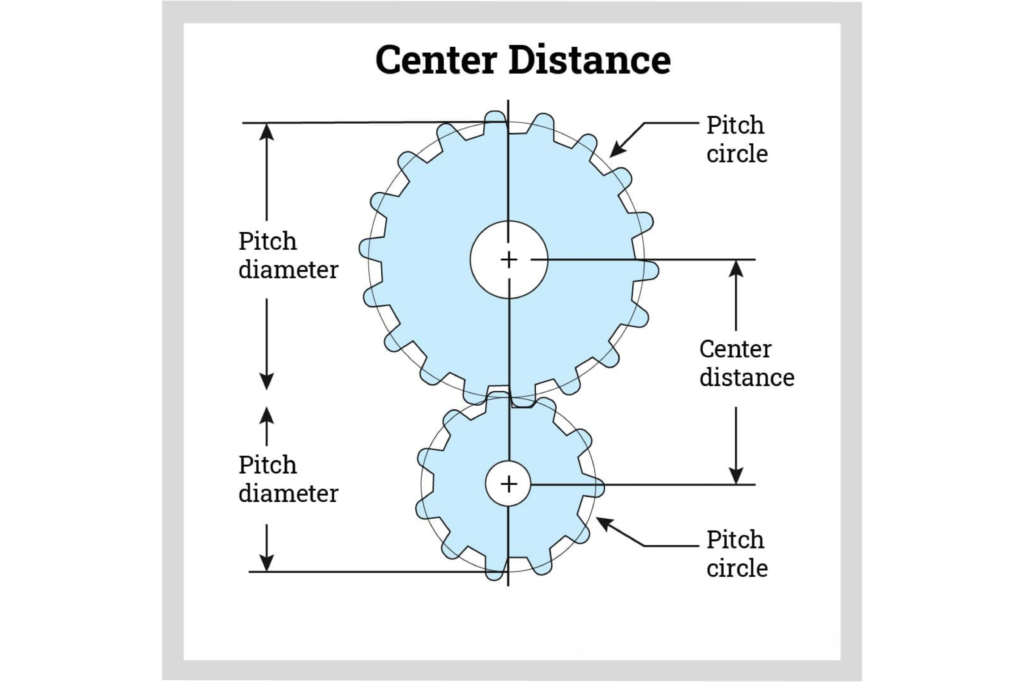
Why are pitch circles important?
Pitch circle is important due to the following factors.
- Synchronized Movement: It ensures that two grooved rollers are working together.
- Calculating Relative Speeds: Pitch circle is used to calculate the speed of one roller relative to another for smooth crushing operation.
- Not just one roller: MED is about only one roller working. However the Pitch Circle defines synchronisation of multiple rollers.
What is a Tooth profile Arrangement?
Tooth Profile is the shape and characteristic of the grooves on sugar mill rollers.
Tooth Profile Arrangement refers to the pattern and spacing of the grooves. Some common factors are:
- Pitch: The distance between the centers of two adjacent grooves.
- Depth: How deep the grooves are cut into the roller surface.
- Helix Angle: Helix angle is the angle at which the grooves are cut. This angle aids in cane feed, juice drainage and reduced corrosion.
Some common Tooth profiles are:
- V-grooves: It is the most common. They provide good cane grip and juice drainage. The angle of the “V” can vary.
- U-grooves: They are used when different gripping and drainage properties are required.
- Serrations/Knurling: They are the finer patterns applied on top of the rollers. They are used instead of larger grooves
The Tooth profile determines:
- Cane Gripping
- Juice Drainage
- Fibre Collection
Sugar Mill Roller Setting Calculations
What is the data required for calculations?
Calculation of accurate Mill setting requires the following data:
- Fiber % in Cane: This represents the percentage of insoluble fiber in the sugarcane. Typical values range from 12-16%.
- Roll Diameters: The physical outer diameter of the roller in mm.
- Roller Length: The physical length of the roller in mm.
- Cane Throughput: The rate at which sugarcane is processed. It is measured in Tons Cane per Hour.
- Speed of Rotation: The rotational speed of the rollers. It is typically in Revolutions Per Minute.
How to calculate fiber rate?
How to calculate Mill roller surface speed?
Formula for setting calculation based on MED and work openings?
Step-by-Step Sugar Mill Roller Setting Calculation:
Discharge Work Opening Calculation:
Actual Discharge Work Opening Calculation:
Feed opening calculation:
Actual Feed Work Opening Formula:
Actual Feed Work Opening = Feed Work Opening – Roller Rise
Trash Plate Opening Calculation:
Trash plate opening involves two clearances:
- Feed-Side Trash Plate Opening: It is the gap between the trash plate and the feed roller. This gap is kept wider.
- Discharge-Side Trash Plate Opening: It is the gap between the trash plate and the discharge roller. This gap is kept very tight.
Trash plate mill settings are determined by the manufacturer recommendations. Furthermore, they can also be adjusted by observing mill performance and precise theoretical formulas. Still, it is a challenging task.
Setting Adjustment Process
Instructions for Setting a Mill
The following steps should be followed for setting a mill.
- Cleaning:
Sugar mill rollers and trash plates should be cleaned before any adjustments. Cleaning means that any residual bagasse should be removed.
- Removing the gaps:
- Top Roller Position: The top roller should be at the lowest possible position, without any cane in the mill.
- Measure Physical Gaps: Feeler gauges are used to measure the physical gaps between the feed roller and the top roller. Also measure the gap between the discharge roller and the top roller.
- Hydraulic System: hydraulic pressure systems should be capable of applying accurate pressures.
- Calculating Settings:
Calculate the fiber percentage, cane throughput, roller speeds, and MED for accurate mill settings. These calculations lead to accurate positioning of feed opening, discharge opening, and trash plate settings.
- Verification:
Re-measure all the gaps to ensure they match the desired initial values.
Tools and Instruments Required
The tools required for mill settings include:
- Feeler Gauges: They are used for precisely measuring the gap between the rollers.
- Measuring Tapes: They are used to measure larger dimensions like roller diameters.
- Hydraulic Pressure Gauges: They are used to monitor and adjust the hydraulic load that is applied to the top roller.
- Spirit Levels/Laser Levels: They are used to ensure that the rollers are accurately levelled and parallel.
- Theodolites or Laser Alignment Tools: They are used for modern, precise alignment of roller axes.
- Torque Wrenches: They are used to tighten the bolts and lock mechanisms to specific torque values.
- Mill Setting Calculation Software/Sheets: They are used to perform the complex calculations for optimal mill setting.
Monitoring and Adjustments
Mill settings require continuous monitoring and adjustments to ensure a smooth operation. Below are some signs that indicate the need for adjustment of the mill setting.
- Reduced Juice Extraction Efficiency: Low juice extraction is indicated by two conditions. If the juice extracted is either lower than expected sucrose in juice or higher than acceptable sucrose in bagasse. Under this condition mill setting adjustment is needed.
- High Bagasse Moisture: If the bagasse feels too wet, it indicates that the compression is insufficient. Under this condition mill setting adjustment is needed. Typical bagasse moisture content aims for 48-52%.
- Mill Choking: Frequent jams in the nip indicates the inaccurate distance between the rollers. Under this condition mill setting adjustment is needed.
- Excessive Power Consumption: Increased power consumption by the roller motors indicate inefficiency. Under this condition mill setting adjustment is needed.
- Roller Slippage/Chattering: The slippage of cane between the rollers suggests insufficient grip. Under this condition mill setting adjustment is needed.
- Uneven Bagasse Blanket: A non-uniform bagasse blanket indicates uneven roller pressure distribution. Under this condition mill setting adjustment is needed.
Adjustment Procedures During Operation
- Hydraulic Load Adjustments: The most common adjustment is varying the hydraulic pressure that pushes the top roller down. Hydraulic Load is increased for effective nipping.
- Trash Plate Adjustments: The trash plate’s position is adjusted to deal with issues of guiding, re-absorption, or choking.
- Roller Speed Changes: In modern mills, individual roller speeds are tuned to improve feeding and reduce slippage.
- Periodic Re-measurement: These are the physical checks made to ensure the optimized working of the mill.
Troubleshooting & Optimization: Mill Setting
Despite accurate mill settings, sugar mills still require continuous inspections. Inspections are crucial for high efficiency.
Common Setting Issues
The following are some common issues faced by sugar mills operations.
- Excessive Juice Loss:
Low juice extraction is indicated by two conditions. If the juice extracted is either lower than expected sucrose in juice or higher than acceptable sucrose in bagasse. The root cause is the inaccurate distance between the rollers.
- High Bagasse Moisture:
The bagasse that exits the mill is overly wet. This indicates incomplete juice extraction. The root cause is a larger nip distance.
- Cane Slippage:
The rollers fail to grip and push the sugarcane into the mill. The root cause is when the feed opening is too wide.
Achieving Optimal Settings
Regular Maintenance, Operator training, and Data Analysis are among the best practices to achieve optimal mill settings.
- Regular Maintenance: You should continuously inspect the rollers corrosion, alignment, and hydraulic loads.
- Operator Training: Highly trained and experienced operators can analyze the mill operations and make quick decisions.
- Data Analysis: You should keep detailed records of settings, cane quality, and extraction performance. By analyzing this data, effective decisions can be made.
Conclusion
Thus, sugar mill roller settings are important for operational success. Precise nip, MED, and work openings are calculated for efficient sugar mills. Still, continuous monitoring and troubleshooting are vital for achieving and maintaining peak performance.
Being an expert Sugar Mill Roller Chinese Manufacturer, we offer you customized sugar mill rollers. Choose us for your sugar mill rollers that promise superior performance, unmatched durability, and secure your future. Partner with us to enhance your mill’s productivity.